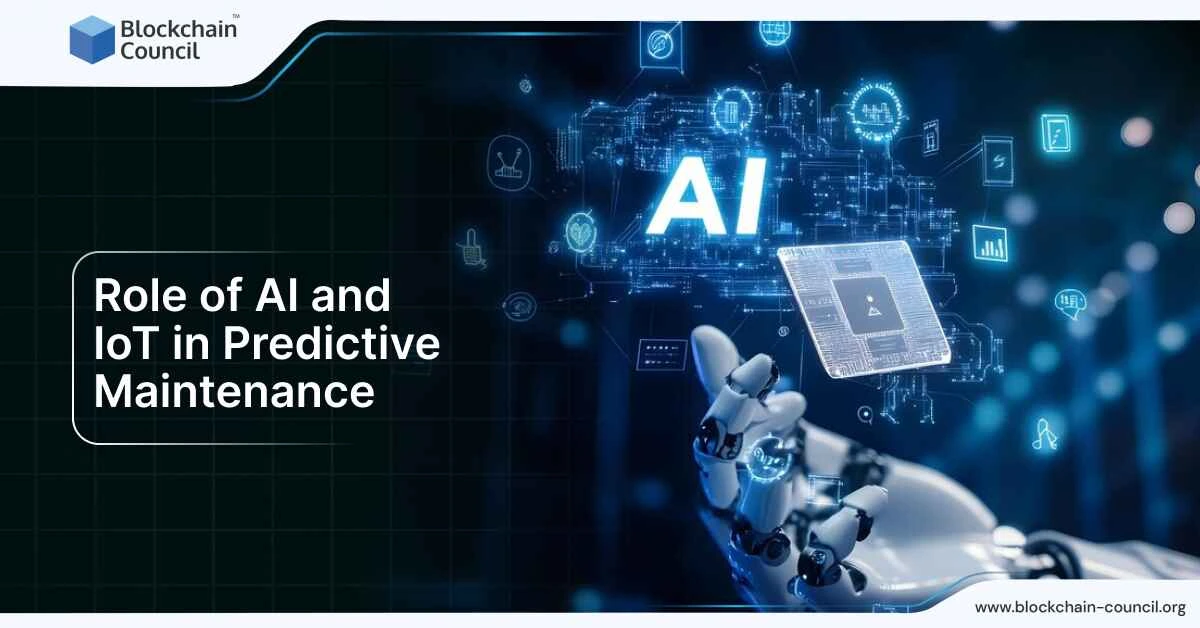
- Blockchain Council
- December 20, 2024
Artificial Intelligence (AI) and the Internet of Things (IoT) are creating big changes in the manufacturing sector. They’ve made it possible to predict equipment issues before they happen. This means repairs can be planned ahead, saving time and cutting down on costs. By combining AI with IoT tools, businesses can watch machines in real-time, check how they’re performing, and address problems before they turn into major breakdowns.
What Predictive Maintenance Is All About
Predictive maintenance uses data to spot unusual patterns and guess when equipment might fail. Traditional approaches usually involve fixing machines only after something goes wrong or performing routine check-ups regardless of need. Predictive maintenance takes a smarter route, relying on actual equipment conditions. This helps ensure maintenance happens only when it’s truly required, saving time and making better use of resources.
How AI Makes Predictive Maintenance Smarter
AI plays a huge role in making predictive maintenance more effective. It processes large volumes of information from equipment, picking up patterns and signs of trouble. Using machine learning, AI can study past data and anticipate future problems. For example, a solution by Siemens uses AI to create behavior models for machinery, helping businesses focus their attention on specific areas. Generative AI has even added another layer of convenience by enabling smoother conversations between users and experts, making it easier to decide on the next steps.
The Role of IoT in Predictive Maintenance
IoT gadgets like sensors collect up-to-the-second data about machine health. These tools help track how equipment is functioning and allow immediate action when needed. In factories, smart IoT systems combined with AI can monitor machinery closely, adjust operations, and ensure safety while improving overall output. To know more about AI and its impact on predictive maintenance, consider getting expert-led AI certifications by the Blockchain Council.
Real-Life Success Stories
Many organizations are already using AI-driven predictive maintenance successfully:
- Holcim: This building materials company uses AI across over 100 locations to foresee and prevent equipment problems. This has improved both efficiency and reliability in its operations.
- Priestley’s Gourmet Delights: A bakery in Australia has invested $53 million in a modern factory with AI-powered tools. These upgrades have increased production capacity while cutting down on manual labor.
- Qantas: The airline uses AI to plan fuel usage, optimize flight routes, and manage unexpected challenges. Predictive maintenance also ensures their aircraft operate reliably, keeping both costs and risks low.
Why AI-Driven Predictive Maintenance Works
This approach brings multiple advantages for businesses:
- Less Unplanned Downtime: By catching problems early, companies can choose the best time for repairs. This prevents unexpected interruptions.
- Cost Efficiency: Planning repairs ahead of time avoids expensive breakdowns and helps extend the life of machines.
- Better Workplace Safety: Spotting and addressing issues early lowers the chances of accidents caused by faulty equipment.
- Increased Productivity: Machines that are well-maintained produce better results, leading to happier customers and higher output.
Hurdles in Adopting AI-Driven Predictive Maintenance
Although it’s highly effective, there are challenges to putting this system into place:
- Data Reliability: AI models need accurate and relevant information to make correct predictions. Ensuring this level of quality is often challenging.
- Merging with Current Systems: Adding AI to existing setups can be tricky and may require large investments.
- Skill Gaps: Employees need specialized knowledge to handle AI tools. This often means extra training and development for the workforce.
What Lies Ahead
As technology continues to improve, more industries will adopt AI and IoT solutions for maintenance. These systems are becoming easier to use and more affordable. Over time, businesses can expect higher efficiency, better safety, and reduced costs. The future points to smarter systems that can both monitor and improve operations instantly.
Wrapping Up
AI and IoT are reshaping the manufacturing world by enabling smarter maintenance practices. Examples from companies like Holcim, Priestley’s Gourmet Delights, and Qantas prove just how effective these solutions can be. With less downtime, lower expenses, and improved safety, adopting AI-driven predictive maintenance is quickly becoming a must for businesses aiming to thrive. The journey forward is clear—embracing smarter technologies will lead to success and better results.